Quality Culture
Unicorn is committed to delivering high quality products and services in the display industry. We demonstrate our ongoing commitment to quality by continually promoting mindset of "defect-free" within our organization. The quality culture within the organization not only encourages our employees to put the best effort for their day to day work, but also empowers our employees to proactively engage in activities towards quality excellence. Based on this foundation, we are able to relentlessly create value for our customers and achieve high level of customer satisfaction.
Quality Management System
Unicorn has strong belief that continual growth of business, long term partnership and relationship shall be highly attributed to not only to stability of product quality and consistency of service, but also demonstration of continual improvement. A well-established quality management system has fundamentally allowed us to rightfully plan our value-added process, systematically control and improve our processes and products so as to ultimately ensure high level of customer satisfaction.

Establish and maintain an integral quality management system compliant with ISO9001 and IATF16949 as well as standards recognized by the industry.

Develop products that meet customers’ needs through advanced planning in design and development cycle, as well as emphasizing the concept of build-in quality.

Establish manufacturing processes integrating product and process control measures, orientated with error prevention, robust monitoring and closed loop control mechanism.

Apply systematic analysis and problem solving methodology for process characterization, variation minimization, defect reduction and improvement deployment.

Continuously improve effectiveness of entire management system and value added processes in order to deliver quality products and enhance values for our customers.

Quality Control
Unicorn is equipped with state-of-the-art LCD and LCM manufacturing equipment, “industrial strength” control processes, in-process detection system, comprehensive inspection and testing plan.

Material Quality Control
1. Materials are purchased only from qualified and approved sources or suppliers.
2. Incoming inspection plan for cosmetic, form & dimension, functionality, shelf-life & packing.
3. Zero acceptance sampling plan for incoming materials and parts
4. Verification plan and sampling test to ensure compliance of material substance with hazardous substance (ROHS/ELV) requirement.
5. Tailored storage environment to cater for various materials, supported with real time surveillance system for storage condition.

Process Quality Control
1. Automated equipment and production lines for LCD front-of-line (FOL), middle-of-line (MOL), and Module lines (LCM).
2. Cleanroom shop-floors and workstations with ISO Class 5, Class 6 and Class 7.
3. Poka-yoke control and error detection system widely installed across manufacturing processes
4. Job change-over verification, first-piece inspection, in-station inspection, last-piece inspection, statistical process control (SPC).
5. Product traceability system
6. ESD protection and control according to ESD 20.20

Product Quality Control
1. 100% semi-finished product inspection and testing
2. 100% finished product inspection and testing
3. 100% OQC (Outgoing Quality Control) inspection plan for automotive products
4. Zero acceptance sampling plan at OQC.
5. Aging screening test
6. Product reliability test for pre-launch production
7. Ongoing reliability test (ORT)
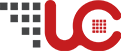
Unicorn Electronic (Shenzhen) Co., Ltd
No.214 of AnLan Road,Zhang Keng Jing Village,GuanHu Street,Longhua District,ShenZhen,PRC
© Copyright 2024 Unicorn Electronic (Shenzhen) CO., LTD. All rights reserved. | Privacy policy